In den letzten Jahren hat die industrielle Produktion einen intensiven Prozess zur Steigerung der Produktivität und Qualität durchlaufen. Bisherige Optimierungsansätze haben jedoch bereits kein Potenzial mehr, die Produktion zu verbessern, und die 4. industrielle Revolution kam auf die Bühne. Die Digitalisierung spielt heute die wichtigste Rolle bei der Optimierung der Produktion.
Durch die Digitalisierung der Produktion erhält das Unternehmen genauere und zuverlässigere Daten zum Verlauf des Produktionsprozesses. Auf dieser Grundlage kann das Unternehmen Produktionsprozesse effizienter einrichten, die Produktivität steigern, die Kosten erheblich senken und insbesondere die Innovation in der Produktion beschleunigen.
Neue digitale Technologien verändern das Umfeld der industriellen Produktion radikal und werden auch die Wettbewerbsfähigkeit von Unternehmen erheblich beeinflussen. Angesichts dieser Herausforderung ist die Digitalisierung keine Frage mehr, sondern eine Notwendigkeit für alle Unternehmen, die weiterhin nachhaltig und wettbewerbsfähig arbeiten möchten.
Die Technologie des Digitalen Zwillings
Eine der wichtigsten Technologien zur Digitalisierung der Produktion ist ein Digitaler Zwilling. Der Digitale Zwilling ist ein genaues virtuelles Modell eines Produkts oder einer Produktionslinie. Es besteht aus mehreren Elementen wie Fertigungssimulationen, 3D-CAD-Modellen und Echtzeit-Datenfeeds von Sensoren, die in die physische Betriebsumgebung integriert sind.
Der Digitale Zwilling zeichnet Änderungen während des gesamten Lebenszyklus auf und bewertet sie. So können Unternehmen Verhalten vorhersagen, Engpässe und ineffiziente Abläufe identifizieren und die Produktion optimieren. Darüber hinaus können verschiedene Änderungen und Innovationen simuliert und getestet werden, bevor sie in Betrieb genommen werden, wodurch ihre zuverlässige und kosteneffiziente Implementierung sichergestellt wird. Einfach ausgedrückt kann ein Digitaler Zwilling praktisch alles „vorhersehen“, was in der realen Produktion passieren kann.
Der Digitale Zwilling macht jeden Prozess effizienter
Die Vorteile von des Digitalen Zwillings enden jedoch nicht in der Optimierung der Produktionsprozesse. Er stellt auch eine große Chance für die Produktion auf der Ebene von Engineering, Designanpassung, Prozessen, Betrieb und Wartung dar.
Engineering – Unter diesem Begriff verstehen wir das Design und die Verbesserung von Produkten mithilfe von CAD-Programmen. Mit Hilfe eines Digitalen Zwillings ist es möglich, wichtige Informationen direkt vor Ort aufzuzeichnen. Basierend auf diesen Informationen können Sie Analysen in einem Simulationsmodell durchführen und so das Produkt ständig verbessern.
Anpassen des Designs – Stellen Sie sich vor, Sie können Ihren Kunden Ihre Produkte in verschiedenen Modifikationen anbieten, die genau ihren Anforderungen entsprechen (unterschiedliche Farben, Leistungen usw.). Wenn Sie diese Änderungen in einem Digital Twin vornehmen, erhalten Sie ein umfassenderes Bild der Auswirkungen der Änderung der Produktkonfiguration auf die Kosten und können kostspielige Fertigungsmodifikationen vermeiden, die möglicherweise nicht effizient sind.
Produktion – Die Produktion kann vor der endgültigen Installation auf Verteilung, Materialflüsse und Prozesse getestet werden. Der Digitale Zwilling ermöglicht eine „Ansicht“ des gesamten Modells und beschleunigt so auch die Kommunikation zwischen einzelnen Teams in der Produktion.
Betriebsprozesse – Mit dem Digitalen Zwilling in Betriebsprozessen ist es möglich, die tatsächlichen Produktionszahlen in Echtzeit zu erfassen und neu zu berechnen, sodass Sie aus den tatsächlichen Produktionszahlen Prognosen der Trends erstellen können. Auf diese Weise können Sie sofort auf bevorstehende Änderungen in der Produktion reagieren und die langfristigen Ergebnisse dieser Änderungen vorhersagen.
Wartung – Mit dem Digitalen Zwilling können Sie auch die sogenannte „vorausschauende Wartung“ realisieren. Mit der Verwendung von Sensoren kann man ungewöhnliches Verhalten von Maschinen und Anlagen (Vibrationen, Abweichungen im Maschinenbetrieb) erkennen, bevor diese Abweichungen bei einer Nichtkonformität der Produkte sichtbar werden, und Sie können reagieren, bevor ein Maschinenausfall auftritt.
Das Digital Twin-Konzept
Das Wesconi Digital Twin-Konzept besteht aus 3 Teilen:
1. Digital Twin des Produkts
Der Digitale Zwilling des Produkts umfasst das Produktdesign sowie die virtuelle, systemorientierte Produktentwicklung. Dies ermöglicht das umfassende Entwerfen, Simulieren und Validieren von Produkten, das Automatisieren des elektronischen Designs und des Softwaremanagements in allen Bereichen der Entwicklung, ohne dass physische Prototypen erforderlich sind.
2. Digital Twin der Produktion
Produktionsplanung in einer digitalen Umgebung, Simulation, Optimierung und automatische Generierung eines Programms zur SPS-Steuerung schaffen einen digitalen Zwilling der Produktion. Die miteinander verbundene Simulation von Mechanik- und Automatisierungsteilen erfasst das endgültige Verhalten der Maschinen und bildet die Grundlage für die virtuelle Inbetriebnahme.
3. Performance Digital Twin
Mit Hilfe gezielter integrierter Geräte im Betrieb ist es möglich, durch Lesen von Daten aus Produktionslinien und Produkten einen umfassenden Überblick über die Produktion zu erhalten. Dank integrierter Automatisierungselemente können Produktionstechnologien Daten bereitstellen und diese dann auf verschiedenen Ebenen bis hin zur Ebene des Produktdesigns an die Wertschöpfungskette senden. Auf diese Weise schaffen sie einen geschlossenen Kreislauf von Entscheidungsprozessen und die Optimierung der Produkt- und Produktionslinien in Echtzeit.
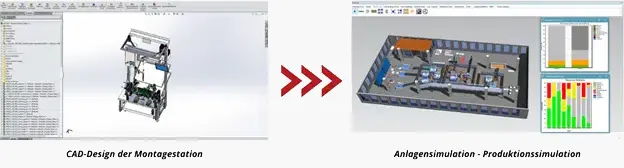
Wie implementieren wir einen Digital Twin in Ihrer Produktion?
- Wir analysieren Ihre aktuellen Produktionsprozesse und schlagen die optimale Lösung für deren Digitalisierung vor.
- Wir werden einen digitalen Fingerabdruck jedes Produkts bereitstellen und mithilfe von IoT-Technologien spezifische Produktionsparameter und den Status des gesamten Produktionsprozesses aufzeichnen.
- Wir werden eine digitale Verbindung einzelner Elemente des Produktionsprozesses und insbesondere einen wechselseitigen Informationsfluss zur und von der Produktion herstellen.
- Wir erstellen einen Überblick darüber, wo Verluste oder Ausfallzeiten auftreten, und schlagen Lösungen vor, um diese zu beseitigen und den Produktionsprozess zu optimieren.
- Wir können das Produkt oder den Produktionsprozess nach Ihren Wünschen ändern. Wir werden ein virtuelles Modell erstellen, in das wir die erforderlichen Änderungen einbeziehen, ohne dass kostspielige Unterbrechungen der tatsächlichen Produktion erforderlich sind.
- We are able to modify the product or production process according to your preferences. We will create a virtual model on which we will incorporate the required changes without the need for costly interruptions of actual production.
- Virtuelle Inbetriebnahme – Vor der Inbetriebnahme prüfen wir, ob das gesamte System mit mechanischen, elektrischen und automatisierten Komponenten wie geplant zusammenarbeitet.
- Erst nach einer gründlichen Prüfung der Änderungen im virtuellen Modell und der Optimierung einzelner Parameter erfolgt die Anwendung von Änderungen auf die reale Produktion.
Die Digitalisierung der Produktion ist ein komplexer Prozess, der zunächst sorgfältig durchdacht und geplant werden muss. Aber wo soll ich anfangen? Was sind die Eintrittskosten? Wie bereite ich ein Unternehmen vor und schule Mitarbeiter? Wir helfen Ihnen gerne weiter und schlagen Ihnen eine optimale Lösung für die Digitalisierung Ihrer Fabrik vor. Kontaktieren Sie uns.